Corrosion behavior of selective laser melting-manufactured bio-applicable 316L stainless steel in ionized simulated body fluid
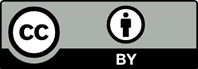
Additive manufacturing (AM) is gaining increasing popularity in various fields, including biomedical engineering. Although AM enables fabrication of tailored components with complex geometries, the manufactured parts typically feature several internal issues, such as unpredictable distribution of residual stress and printing defects. However, these issues can be reduced or eliminated by post-processing via thermomechanical treatment. The study investigated the effects of combinations of AM and post-processing by the intensive plastic deformation method of rotary swaging (variable swaging ratios) on microstructures, residual stress, and corrosion behaviors of AISI 316L stainless steel workpieces; the corrosion tests were performed in an ionized simulated body fluid. The results showed that the gradual swaging process favorably refined the grains and homogenized the grain size. The imposed swaging ratio also directly influenced the development of substructure and dislocations density. A high density of dislocations positively affected the corrosion resistance, whereas annihilation of dislocations and formation of subgrains had a negative effect on the corrosion behavior. The first few swaging passes homogenized the distribution of residual stress within the workpiece and acted toward imparting a predominantly compressive stress state, which also favorably influenced the corrosion behavior. Lastly, the presence of the {111}||swaging direction texture fiber (of a high intensity) increased the resistance to pitting corrosion. Overall, the most favorable corrosion behavior was acquired for the AM sample subjected to the swaging ratio of 0.8, exhibiting a strong fiber texture and a high density of dislocations.
- Jalali M, Mohammadi K, Movahhedy MR, et al. SLM additive manufacturing of NiTi porous implants: A review of constitutive models, finite element simulations, manufacturing, heat treatment, mechanical, and biomedical studies. Met Mater Int. 2023;29:2458-2491. doi: 10.1007/s12540-023-01401-1
- Kazantseva N, Krakhmalev P, Yadroitsev I, et al. Oxygen and nitrogen concentrations in the Ti-6Al-4V alloy manufactured by direct metal laser sintering (DMLS) process. Mater Lett. 2017;209:311-314. doi: 10.1016/j.matlet.2017.08.037
- Dzogbewu TC, Amoah N, Fianko SK, Afrifa Jnr S, de Beer D. Additive manufacturing towards product production: A bibliometric analysis. Manuf Rev. 2022;9:1. doi: 10.1051/mfreview/2021032
- Paul AC, Jinoop AN, Paul CP, Deogiri P, Bindra KS. Investigating build geometry characteristics during laser directed energy deposition based additive manufacturing. J Laser Appl. 2020;32(4):042002. doi: 10.2351/7.0000004
- Wang Z, Zhang Y, Bernard, A. A constructive solid geometry-based generative design method for additive manufacturing. Addit Manuf. 2021;41(4):101952. doi: 10.1016/j.addma.2021.101952
- Weyhrich CW, Long TE. Additive manufacturing of high-performance engineering polymers: Present and future. Polym Int. 2022;71(5):532-536. doi: 10.1002/pi.6343
- Nefedovaa LA, Ivkov VI, Sychov MM, Lebedev LA, Dyachenko SV. Additive manufacturing of ceramic insulators. Mater Today Proc. 2020;30(2):520-522. doi: 10.3390/ma16134636
- Sotov A, Kantyukov A, Popovich A, Sufiiarov V. A review on additive manufacturing of functional gradient piezoceramic. Micromachines. 2022;13(7):1129. doi: 10.3390/mi13071129
- Moreno Madrid AP, Vrech SM, Sanchez MA, Rodriguez AP. Advances in additive manufacturing for bone tissue engineering scaffolds. Mater Sci Eng C. 2019;100(15): 631-644. doi: 10.1016/j.msec.2019.03.037
- Dzogbewu TC. Laser powder bed fusion of Ti6Al4V lattice structures and their applications. J Met Mater Miner. 2020;30(4):68-78. doi: 10.55713/jmmm.v30i4.821
- Mohammed A, Jiménez A, Bidare, P, et al. Review on engineering of bone scaffolds using conventional and additive manufacturing technologies. 3D Print Addit Manuf. 2023;[online]. doi: 10.1089/3dp.2022.0360
- Yamashita Y, Murakami T, Mihara R, Okada M, Murakami Y. Defect analysis and fatigue design basis for Ni-based superalloy 718 manufactured by additive manufacturing. Procedia Struct Integr. 2017;7:11-18. doi: 10.1016/j.prostr.2017.11.054
- Hoefer K, Mayr P. Additive manufacturing of titanium parts using 3D plasma metal deposition. Mater Sci Forum. 2018;941:2137-2141. doi: 10.4028/www.scientific.net/MSF.941.2137
- Mclean N, Bermingham MJ, Colegrove P, et al. Effect of hot isostatic pressing and heat treatments on porosity of wire arc additive manufactured Al 2319. J Mater Process Technol. 2022;310:117769. doi: 10.1016/j.jmatprotec.2022.117769
- Shakil SI, Smith NR, Yoder SP, et al. Post fabrication thermomechanical processing of additive manufactured metals: A review. J Manuf Process. 2022;73:757-790. doi: 10.1016/j.jmapro.2021.11.047
- Kunčická L, Kocich R, Németh G, Dvořák K, Pagáč M. Effect of post process shear straining on structure and mechanical properties of 316 L stainless steel manufactured via powder bed fusion. Addit Manuf. 2022;59(A):103128. doi: 10.1016/j.addma.2022.103128
- Kunčická L, Kocich R, Benč M, Dvořák J. Affecting microstructure and properties of additively manufactured AISI 316L steel by rotary swaging. Materials. 2022;15(18):6291. doi: 10.3390/ma15186291
- Han W, Fang F. Eco-friendly NaCl-based electrolyte for electropolishing 316L stainless steel. J Manuf Process. 2020;58:1257-1269.
- Lee SK, Yun S-H, Joo HG, Noh SJ. Deuterium transport and isotope effects in type 316L stainless steel at high temperatures for nuclear fusion and nuclear hydrogen technology applications. Curr Appl Phys. 2014;14(10):1385-1388. doi: 10.1016/j.cap.2014.08.006
- Lin K, Qiao J, Gu D, et al. Active screen plasma nitriding of laser powder bed fusion processed 316L stainless steel for the application of fuel cell bipolar plates. Virtual Phys Prototyp. 2023;18(1):e2225490. doi: 10.1080/17452759.2023.2225490
- Romanovski V, Frantskevich V, Kazlouski V, et al. Inappropriate cleaning treatments of stainless steel AISI 316L caused a corrosion failure of a liquid transporter truck. Eng Fail Anal. 2020;117:104938. doi: 10.1016/j.engfailanal.2020.104938
- Brooks EK, Brooks RP, Ehrensberger MT. Effects of simulated inflammation on the corrosion of 316L stainless steel. Mater Sci Eng C. 2017;71:200-205. doi: 10.1016/j.msec.2016.10.012
- Kunčická L, Kocich R, Lowe TC. Advances in metals and alloys for joint replacement. Prog Mater Sci. 2017;88:232- 280. doi: 10.1016/j.pmatsci.2017.04.002
- Kong D, Ni X, Dong C, et al. Heat treatment effect on the microstructure and corrosion behavior of 316L stainless steel fabricated by selective laser melting for proton exchange membrane fuel cells. Electrochim Acta. 2018;276:293-303. doi: 10.1016/j.electacta.2018.04.188
- Kocich R, Kunčická L, Macháčková A. Twist channel multi-angular pressing (TCMAP ) as a method for increasing the efficiency of SPD. IOP Conf Ser Mater Sci Eng. 2014;63:012006. doi: 10.1088/1757-899X/63/1/012006
- Jamili AM, Zarei-Hanzaki A, Abedi HR, Mosayebi M, Kocich R, Kunčická L. Development of fresh and fully recrystallized microstructures through friction stir processing of a rare earth bearing magnesium alloy. Mater Sci Eng A. 2019;775:138837. doi: 10.1016/j.msea.2019.138837
- Hemmasian Ettefagh A, Guo S, Raush J. Corrosion performance of additively manufactured stainless steel parts: A review. Addit Manuf. 2021;37:101689. doi: 10.1016/j.addma.2020.101689
- Majumdar JD, Kumar A, Pityana S, Manna I. Laser surface melting of AISI 316L stainless steel for bio-implant application. Proc Natl Acad Sci: Phys Sci. 2018;88:387-403. doi: 10.1007/s40010-018-0524-4
- Saboori A, Aversa A, Marchese G, Biamino S, Lombardi M, Fino P. Microstructure and mechanical properties of AISI 316L produced by directed energy deposition-based additive manufacturing: A review. Appl Sci. 2020;10(9):3310. doi: 10.3390/app10093310
- Guo P, Zou B, Huang C, Gao H. Study on microstructure, mechanical properties and machinability of efficiently additive manufactured AISI 316L stainless steel by high-power direct laser deposition. J Mater Process Technol. 2017;240:12-22. doi: 10.1016/j.jmatprotec.2016.09.005
- Yin H, Song M, Deng P, Li L, Prorok BC, Lou X. Thermal stability and microstructural evolution of additively manufactured 316L stainless steel by laser powder bed fusion at 500-800 ℃. Addit Manuf. 2021;41:101981. doi: 10.1016/j.addma.2021.101981
- Blinn B, Klein M, Gläßner C, Smaga M, Aurich JC, Beck T. An investigation of the microstructure and fatigue behavior of additively manufactured AISI 316L stainless steel with regard to the influence of heat treatment. Metals. 2018;8(4):220. doi: 10.3390/met8040220
- Zanichelli A, Ronchei C, Scorza D, Vantadori S. Fatigue lifetime of both plain and notched specimens made of additively manufactured AISI 316L. J Mater Res Technol. 2022;21: 2532-2546. doi: 10.1016/j.jmrt.2022.10.068
- Abroug F, Monnier A, Arnaud L, Balcaen Y, Dalverny O. High cycle fatigue strength of additively manufactured AISI 316L stainless steel parts joined by laser welding. Eng Fract Mech. 2022;275:108865. doi: 10.1016/j.engfracmech.2022.108865
- Avanzini A. Fatigue behavior of additively manufactured stainless steel 316L. Materials. 2022;16(1):65. doi: 10.3390/ma16010065
- Werner T, Madia M, Zerbst U. Comparison of the fatigue behavior of wrought and additively manufactured AISI 316L. Procedia Struct Integr. 2022;38:554-563. doi: 10.1016/j.prostr.2022.03.056
- Machno M, Franczyk E, Bogucki R, Matras A, Zębala W. Comparative study on the structure and quality of SLM and cast AISI 316L samples subjected to WEDM processing. Materials. 2022;15(3):701. doi: 10.3390/ma15030701
- Polishetty A, Nomani J, Littlefair G. Evaluating and comparing secondary machining characteristics of wrought and additive manufactured 316L stainless steel. Mater Today Proc, 2023;[online]. doi: 10.1016/j.matpr.2023.05.404
- Vinoth V, Sathiyamurthy S, Natarajan U, Venkatkumar D, Prabhakaran J, Prakash KS. Examination of microstructure properties of AISI 316L stainless steel fabricated by wire arc additive manufacturing. Mater Today Proc. 2022;66(7):702-706. doi: 10.1016/j.matpr.2022.04.011
- Zach L, Kunčická L, Růžička P, Kocich R. Design, analysis and verification of a knee joint oncological prosthesis finite element model. Comput Biol Med. 2014;54:53-60. doi: 10.1016/j.compbiomed.2014.08.021
- Pardo A, Merino MC, Coy AE, Viejo F. Pitting corrosion behaviour of austenitic stainless steels – combining effects of Mn and Mo additions. Corros Sci. 2008;50(6):1796-1806. doi: 10.1016/j.corsci.2008.04.005
- Shih C-C, Shih C-M, Su Y-Y, Julie Su LH, Chang M-S, Lin S-J. Effect of surface oxide properties on corrosion resistance of 316L stainless steel for biomedical applications. Corros Sci. 2004;46(2):427-441. doi: 10.1016/S0010-938X(03)00148-3
- Shahryari A, Omanovic S, Szpunar JA. Electrochemical formation of highly pitting resistant passive films on a biomedical grade 316LVM stainless steel surface. Mater Sci Eng C. 2008;28(1):94-106. doi: 10.1016/j.msec.2007.09.002
- Tekdir H, Yetim T, Yetim AF. Corrosion properties of ceramic-based TiO2 films on plasma oxidized Ti6Al4V/316L layered implant structured manufactured by selective laser melting. J Bionic Eng 2021;18:944-957.
- Yetim T, Tekdir H, Taftalı M, Turalıoğlu K, Yetim AF. Synthesis and characterisation of single and duplex ZnO/ TiO 2 ceramic films on additively manufactured bimetallic material of 316L stainless steel and Ti6Al4V. Surf Topogr Metrol Prop. 2023;11(2):024005. doi: 10.1088/2051-672X/accf6c
- Fredriksson W, Petrini D, Edström K, Björefors F, Nyholm L. Corrosion resistances and passivation of powder metallurgical and conventionally cast 316L and 2205 stainless steels. Corros Sci. 2013;67:268-280. doi: 10.1016/j.corsci.2012.10.021
- Geenen K, Röttger A, Theisen W. Corrosion behavior of 316L austenitic steel processed by selective laser melting, hot-isostatic pressing, and casting. Mater Corros. 2017;68(7):764-775. doi: 10.1002/maco.201609210
- Hardes C, Pöhl F, Röttger A, Thiele M, Theisen W, Esen C. Cavitation erosion resistance of 316L austenitic steel processed by selective laser melting (SLM). Addit Manuf. 2019;29:100786. doi: 10.1016/j.addma.2019.100786
- Canelo-Yubero D, Kocich R, Hervoches C, Strunz P, Kunčická L, Kratka L. Neutron diffraction study of residual stresses in a W–Ni–Co heavy alloy processed by rotary swaging at room and high temperatures. Met Mater Int. 2022;28(4):919-930. doi: 10.1007/s12540-020-00963-8
- Oyane A, Onuma K, Ito A, Kim H-M, Kokubo T, Nakamura T. Formation and growth of clusters in conventional and new kinds of simulated body fluids. J Biomed Mater Res. 2003;64(2):339-348. doi: 10.1002/jbm.a.10426
- Oyane A, Kim H-M, Furuya T, Kokubo T, Miyazaki T, Nakamura T. Preparation and assessment of revised simulated body fluids. J Biomed Mater Res. 2003;65(2): 188-195. doi: 10.1002/jbm.a.10482
- Oyane A, Onuma K, Ito A, et al. Variation of clusters in simulated body fluids with time. Key Eng Mater. 2001; 218-220:629-632. doi: 10.4028/www.scientific.net/KEM.218-220.629
- Kořínek M, Halama R, Fojtík F, et al. Monotonic tension-torsion experiments and FE modeling on notched specimens produced by SLM technology from SS316L. Materials. 2020;14(1):33. doi: 10.3390/MA14010033
- Pitassi D, Savoia E, Fontanari V, et al. Finite element thermal analysis of metal parts additively manufactured via selective laser melting. In: Finite Element Method - Simulation, Numerical Analysis and Solution Techniques. 2018. doi: 10.5772/intechopen.71876
- Jin M, Piglione A, Dovgyy B, et al. Cyclic plasticity and fatigue damage of CrMnFeCoNi high entropy alloy fabricated by laser powder-bed fusion. Addit Manuf. 2020;36: 101584. doi: 10.48550/arXiv.2007.07043
- Dovgyy B, Piglione A, Hooper PA, Pham M-S. Comprehensive assessment of the printability of CoNiCrFeMn in laser powder bed fusion. Mater Des. 2020;194:108845. doi: 10.1016/j.matdes.2020.108845
- Elangeswaran C, Cutolo A, Muralidharan GK, et al. Effect of post-treatments on the fatigue behaviour of 316L stainless steel manufactured by laser powder bed fusion. Int J Fatigue. 2019;123:31-39. doi: 10.1016/j.ijfatigue.2019.01.013
- Salman OO, Gammer C, Chaubey AK, Eckert J, Scudino S. Effect of heat treatment on microstructure and mechanical properties of 316L steel synthesized by selective laser melting. Mater Sci Eng A. 2019;748:205-212. doi: 10.1016/j.msea.2019.01.110
- Kunčická L, Macháčková A, Krátká L, Kocich R. Analysis of deformation behaviour and residual stress in rotary swaged Cu/Al clad composite wires. Materials. 2019;12(21):3462. doi 10.3390/ma12213462
- Zhang Q, Jin K, Mu D. Tube/tube joining technology by using rotary swaging forming method. J Mater Process Technol. 2014;214:2085-2094. doi: 10.1016/j.jmatprotec.2014.02.002
- Strunz P, Kunčická L, Beran P, Kocich R, Hervoches C. Correlating microstrain and activated slip systems with mechanical properties within rotary swaged WNiCo pseudoalloy. Materials. 2020;13(1):208. doi: 10.3390/ma13010208
- Wang Z, Chen J, Besnard C, Kuncicka L, Kocich R, Korsunsky AM. In situ neutron diffraction investigation of texture-dependent shape memory effect in a near equiatomic NiTi alloy. Acta Mater. 2021;202:135-148. doi: 10.1016/j.actamat.2020.10.049
- Wang Z, Chen J, Kocich R, et al. Grain structure engineering of NiTi shape memory alloys by intensive plastic deformation. ACS Appl Mater Interfaces. 2022;14(27):31396- 31410. doi 10.1021/acsami.2c05939
- Hervoches C, Mikula P, Vrána M. Recent instrumentation upgrades on the residual strain/stress diffractometer at NPI-Řež, in 53rd International Scientific Conference on Experimental Stress Analysis (EAN 2015), Czech Society for Mechanics, Český Krumlov. 2015;119-120.
- Clausen B, Leffers T, Lorentzen T. On the proper selection of reflections for the measurement of bulk residual stresses by diffraction methods. Acta Mater. 2003;51:6181-6188. doi: 10.1016/j.actamat.2003.07.002
- Zhong Y, Rännar LE, Liu L, et al. Additive manufacturing of 316L stainless steel by electron beam melting for nuclear fusion applications. J Nucl Mater. 2017;486:234-245. doi: 10.1016/J.JNUCMAT.2016.12.042
- Martinez-Perez ML, Mompean FJ, Ruiz-Hervias J, et al. Residual stress profiling in the ferrite and cementite phases of cold-drawn steel rods by synchrotron X-ray and neutron diffraction. Acta Mater. 2004;52:5303-5313. doi: 10.1016/J.ACTAMAT.2004.07.036
- Zhang Y, Chen W, McDowell DL, Y. Wang M, Zhu T. Lattice strains and diffraction elastic constants of cubic polycrystals. J Mech Phys Solids. 2020;138:103899. doi: 10.1016/j.jmps.2020.103899
- Šaroun J, Rebelo-Kornmeier J, Gibmeier J, Hofmann M. Treatment of spatial resolution effects in neutron residual strain scanning. Phys/B. 2018;551:468. doi: 10.1016/J.PHYSB.2018.01.013
- Li G, Song Y, Chen X, et al. Preparation, corrosion behavior and biocompatibility of MgFe-layered double hydroxides and calcium hydroxyapatite composite films on 316L stainless steel. Mater Today Commun. 2023;34:105195
- Mejía-Caballero I, Palomar-Pardavé M, Martínez Trinidad J, et al. Corrosion behavior of AISI 316L borided and non-borided steels immersed in a simulated body fluid solution. Surf Coatings Technol. 2015;280:384-395 doi: 10.1016/j.surfcoat.2015.08.053
- Karimzadeh N, Moghaddam EG, Mirjani M, Raeissi K. The effect of gas mixture of post-oxidation on structure and corrosion behavior of plasma nitrided AISI 316 stainless steel. Appl Surf Sci. 2013;283:584-589. doi: 10.1016/j.apsusc.2013.06.152
- Kocich R, Kunčická L. Optimizing structure and properties of Al/Cu laminated conductors via severe shear strain. J Alloys Compd. 2023;953:170124. doi: 10.1016/j.jallcom.2023.170124
- Beyerlein IJ, Tóth LS. Texture evolution in equal-channel angular extrusion. Prog Mater Sci. 2009;54(4):427-510. doi: 10.1016/j.pmatsci.2009.01.001
- Toth LS, Gilorminis P, Jonas JJ. Effect of rate sensitivity on the stability of torsion textures. Acta Metall. 1988;36(12): 3077-3091. doi: 10.1016/0001-6160(88)90045-4
- Li C, Liu ZY, Fang XY, Guo YB. Residual stress in metal additive manufacturing. Procedia CIRP. 2018;71(2): 348-353. doi: 10.1016/j.procir.2018.05.039
- Macháčková A, Krátká L, Petrmichl R, Kunčická L, Kocich R. Affecting structure characteristics of rotary swaged tungsten heavy alloy via variable deformation temperature. Materials. 2019;12(24):4200 doi: 10.3390/ma12244200
- Kunčická L, Kocich R. Optimizing electric conductivity of innovative Al-Cu laminated composites via thermomechanical treatment. Mater Des. 2022;215(10):110441. doi: 10.1016/j.matdes.2022.110441
- Nazarov AA. Disclinations in bulk nanostructured materials: Their origin, relaxation and role in material properties. Adv Nat Sci Nanosci Nanotechnol. 2013;4:033002. doi: 10.1088/2043-6262/4/3/033002
- Kong D, Dong C, Ni X, et al. Mechanical properties and corrosion behavior of selective laser melted 316L stainless steel after different heat treatment processes. J Mater Sci Technol. 2019;35(7):1499-1507. doi: 10.1016/j.jmst.2019.03.003
- Abbasi Aghuy A, Zakeri M, Moayed MH, Mazinani M. Effect of grain size on pitting corrosion of 304L austenitic stainless steel. Corros Sci. 2015;94:368-376. doi: 10.1016/j.corsci.2015.02.024
- Madrigal-Cano M, Hallen JM, Arce-Estrada EM, Le Manh T. Effect of crystallographic texture and microstructure on pitting corrosion behavior of low carbon steels: A Monte Carlo model. Comput Mater Sci. 2019;161:394-402. doi: 10.1016/j.commatsci.2019.02.016
- Guo D, Kwok CT, Chan SLI. Spindle speed in friction surfacing of 316L stainless steel – How it affects the microstructure, hardness and pitting corrosion resistance. Surf Coatings Technol. 2019;361(2):324-341. doi: 10.1016/j.surfcoat.2019.01.055
- Trisnanto SR, Wang X, Brochu M, Totis G. Effects of crystallographic orientation on the corrosion behavior of stainless steel 316L manufactured by laser powder bed fusion. Corros Sci. 2022;196:110009. doi: 10.1016/j.corsci.2021.110009
- Zhang Y, Cheng F, Wu S. Improvement of pitting corrosion resistance of wire arc additive manufactured duplex stainless steel through post-manufacturing heat-treatment. Mater Charact. 2021;171:110743. doi: 10.1016/j.matchar.2020.110743
- 86. Kunčická L, Kocich R. Effect of activated slip systems on dynamic recrystallization during rotary swaging of electro-conductive Al-Cu composites. Mater Lett. 2022;321(1):10- 13. doi: 10.1016/j.matlet.2022.132436